Diamond Sawed Part Tips & “Rules Of Thumb”
Don’t FORGET to include saw kerf (alley) in part stepping dimensions when making parts.
Saw kerf (blade thickness) recommendations* and limitations:
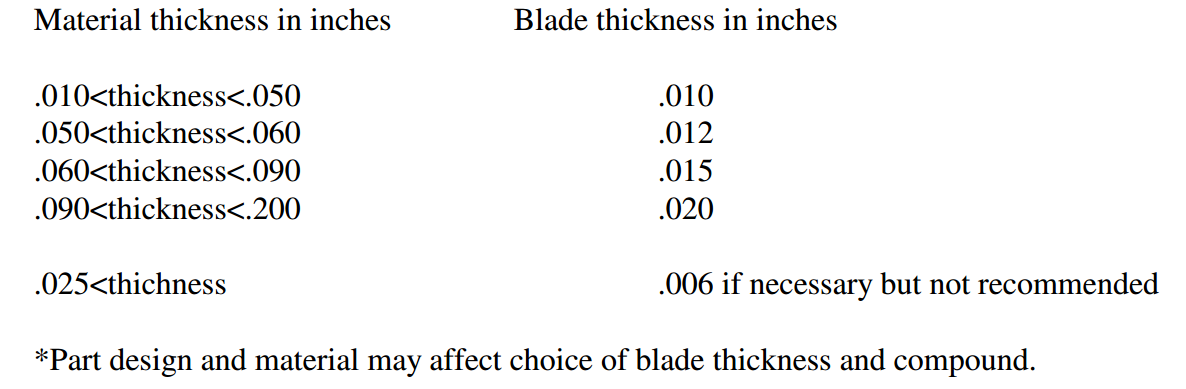
Typical blades (thickness in inches) in stock
.006 .008 .010 .012 .015 .020
Delivery of special blades is typically 4 weeks.
Standard blade thickness tolerances: +/- .0005 inches.
Outside border waste perimeter: .100 inches minimum
Materials exhibiting cut problems:
Molybdenum: bends badly
Bismuth telluride: cut edge quality
Quartz: edge chips
.005 inch thick or less alumina: disintegrates
“Blue Nitto style tape” mount on rings available but avoid using on materials less than .025 inches thick.
Post exposure UV tape mounting is low “tack” for ease of part shipment and removal from tape. The UV de-bond tape is particularly useful for parts that cannot withstand acetone exposure.
UV de-bond type tape mount available but not viable for parts with backside patterns due to poor adhesion.
Both types of tape mountings may offer cost advantages if customer can use parts shipped back still mounted after sawing.
Size limitations: Up to 6 inch diameter, 5.5 inch x 5.5 inch and .215 inches thick.
Avoid mounting of parts with water-soluble adhesives.
Parts MUST be able to withstand immersion in both water and acetone (typically). This limits sawing of many organic materials.
Epoxy bonded (laminated) parts may delaminate in cutting and cleaning process.
Length and width tolerance capability: +/- .001 inches.
Alignment accuracy to pattern feature (excludes run-out in supplied pattern): +/- .001 inches.
Pattern must have sufficient contrast to allow optical alignment.
Smallest cut part size capability: .030 inches x .030 inches.
Alignment targets (features) should NOT be circles. Rectilinear target edges are best.
Typical edge chip limits:
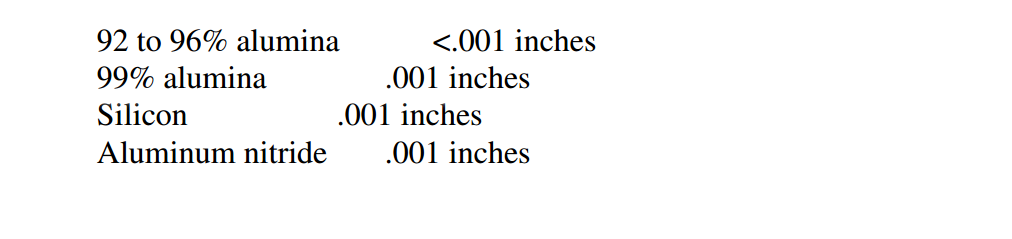